Are Steel Buildings Expensive?
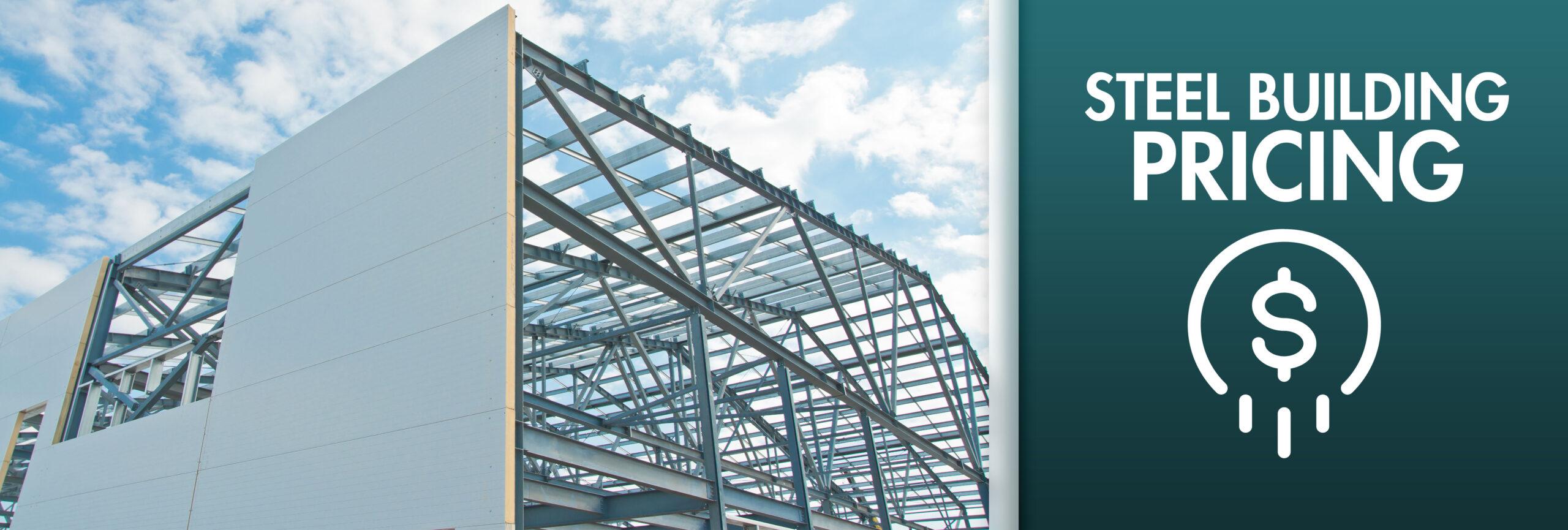
Like anyone who is interested in building with steel, you may be wondering whether pre-engineered steel buildings are more expensive than traditional construction. There is no definitive answer. As with any construction project, costs depend on certain factors.
The initial cost of a steel building kit may be higher than traditional construction with wood and concrete because of the cost of steel versus those materials. However, steel buildings are more cost-effective to install and in the long term, so they are excellent options if you want to build a structure that will stand the test of time.
ROI and Long-Term Value
If you consider the return on your investment and the value you can gain from a metal building, it’s easy to see that it’s much more cost-effective than a traditional build. No wonder the structures are widely used — in fact, industry experts estimate that 70% to 90% of modern construction relies on steel framing or metal.
Durability is one of the reasons steel buildings become extremely cost-effective in the long run. They can withstand earthquakes and high winds and won’t succumb to heavy snowfall. Steel is also non-combustible and doesn’t ignite, ensuring your building can survive fires.  All these features combined make steel buildings an excellent choice, especially in areas prone to natural disasters or forest fires.
And because they are durable, steel buildings won’t require extensive and costly maintenance or repairs. This means you can save even more money down the road.
Cost-Efficiency
The adaptability of steel buildings makes them cost-effective over time. They are low-maintenance and easy to expand, with endless length and width extensions available. Additionally, steel buildings can be insulated more effectively than wood structures. Â There are so many insulation materials and solutions available to boost the energy efficiency of your building, so you can enjoy more savings on cooling and heating costs.
Factors that impact the cost of steel buildings
The price of your steel building can be impacted by the following factors:
- Current market conditions
- Supply and demand
- Oil and gas prices
- Global production
- China’s appetite for steel
Steel prices (like other commodities) are heavily influenced by supply and demand. Global factors — such as China’s increased demand for iron ore and economic recoveries in Europe and the United States —therefore contribute to price volatility.
When dealing with fluctuating steel prices, it’s important to work with a reliable supplier. Â You can count on Armstrong Steel as your trusted partner for high-quality, cost-effective prefabricated steel buildings that meet your business needs.
At Armstrong Steel, we have the luxury of providing steel buildings at extremely competitive prices because when you buy from us, you’re buying directly from a manufacturer — which means you don’t have to pay for the middleman.
Start Saving While Building.
The initial cost of a steel building might be higher than a wood-frame structure, but here at Armstrong Steel Building Systems, we can help you reduce expenses related to fabrication, design, and labor. Here’s how we do it:
Ready to Erect
Pre-engineered steel buildings are generally quick and easy to assemble and erect. This is particularly true for structures that don’t require extensive customizations. In contrast, traditional wood buildings could take at least a few months to finish.
At Armstrong Steel, we ship our steel buildings with a step-by-step erection guide to walk you through the process. Plus, our engineers provide detailed assembly drawings and anchor bolt patterns to remove the guesswork from assembling the parts. All major bolt-together connections are pre-punched to save time and eliminate additional grunt work. Moreover, components are numbered and cut to correspond with the drawings to ensure a streamlined assembly process.
Usage Per Square Foot
Steel beams have significantly more load-bearing capability than wood. For this reason, we can design our steel buildings to have no interior support. You get a wide, open layout that lets you maximize the square footage of your building for any application. Less material is used per square foot of space compared to a wooden structure, too.
Lower Labor Costs
Constructing a steel building is more straightforward than building a traditional wooden structure. Our kits require just a few workers to assemble and erect because all pieces are already pre-cut and punched. Additionally, the erection process is streamlined with detailed drawings and numbered components. All these help our customers reduce their labor costs.
Long-Term Costs
Steel buildings can be completed faster than wooden structures, leading to at least 5% cost savings of your total budget. Thanks to their durability, they will outlast wood structures, too. Our steel buildings can withstand mold, moisture damage, rot, fire, and termite infestations — and all this combined can help reduce your insurance premiums.
Price Your Steel Building Today.
Find out your eligibility for direct pricing and get a quote for general steel buildings here at Armstrong Steel. You may also call 1-800-345-4610 to speak to a friendly building expert who can help you weigh the options.
Popular Posts
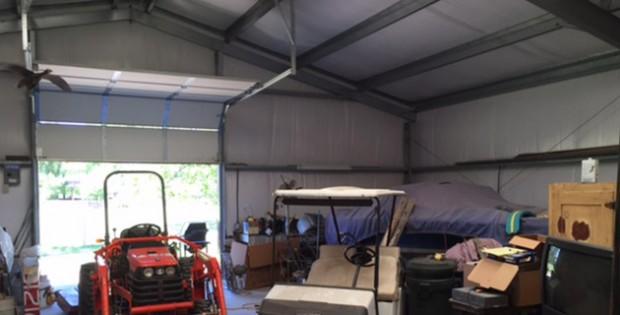
Will Adding a Steel Building Increase My Property Value?
I’ve seen steel buildings increase in popularity every day because builders use these durable, versatile and flexible construction solutions in every application. Not only have homeowners utilized a steel building for residential purposes, but builders have also made additions to their existing property. No doubt that a steel building garage will increase the value of a home,… …
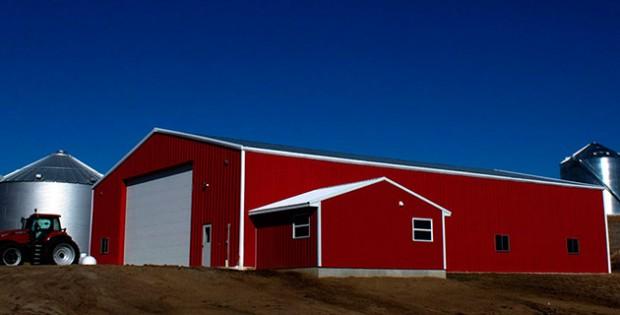
Steel Building Quotes: Get a Grasp on Prices and Estimates
What is the first step of a steel building project, or any construction project for that matter? After you decide to add a new garage, agricultural or commercial building to your property, you’ll most likely start contacting steel building manufacturers for steel building quotes. From there, you can create a timeline for yourself and develop… …
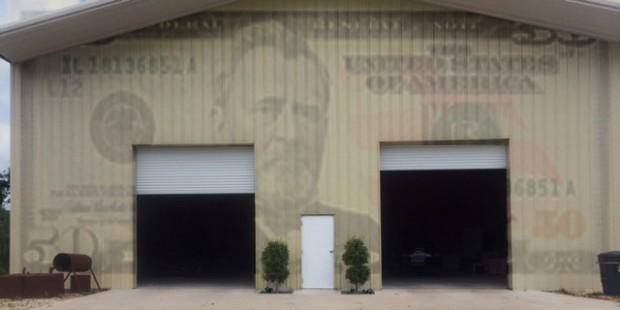
4 Important Factors That Will Impact Your Steel Building Cost
For the past decade, the steel industry has undergone many transformations, and in effect it’s changed the way the construction industry views steel buildings. While the steel itself has been around for hundreds of years, designers and owners of metal buildings are seeing many increased benefits. Because of streamlined processes at manufacturers, energy saving paints… …