How Much Does a Steel Building Cost?
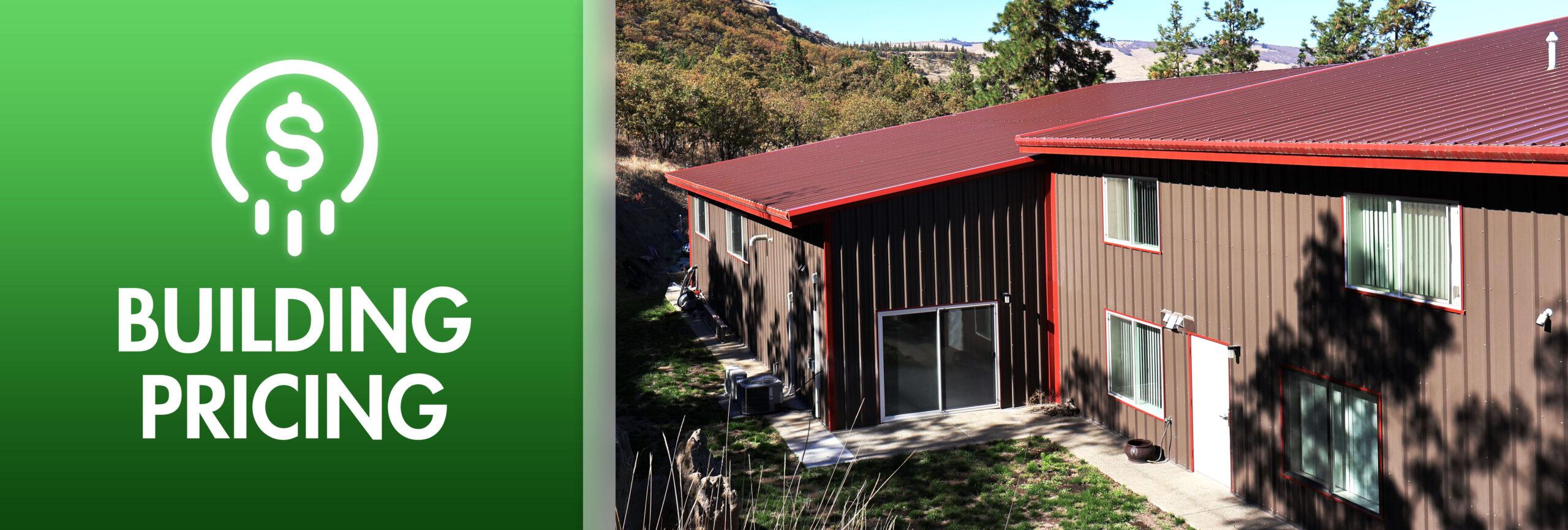
Here at Armstrong Steel, one of the most common questions we receive about our prefabricated steel buildings is about pricing. We offer every customer a spec sheet with the design and inclusions that make up the building price, but there are a lot of factors that go into that price.
When comparing quotes from different fabricators, you’ll likely notice that steel building prices can vary significantly and that price estimates fluctuate over time. In this blog post, we’ll provide insights into the cost of steel buildings from Armstrong Steel and explore the factors that can influence the final price.
Steel buildings vs traditional construction: which is more affordable?
The cost of pre-engineered steel buildings is not generally calculated based on square footage. Steel being a commodity and pre-engineered metal buildings being comprised of many different parts and pieces, pricing a steel building is not that simple. While some companies will throw out an average price range, don’t be fooled, it can vary significantly. This is generally a tactic to attract business. Sure, you could break the price down by square foot, but a 40×60 building with 12-foot walls versus a 40×60 with 18-foot walls simply will not be the same price even though the square footage is the same.
Several factors influence these prices, including global steel prices, supply and demand dynamics, and the specific requirements of your project. It’s best to speak to a true steel building manufacturer for the most accurate and up-to-date pricing information.
That said, steel buildings often offer a better deal when you compare their cost to that of a traditional wood-frame structure. Especially when you must account for the extra costs you should expect from excess material usage.
Rising steel prices
At Armstrong Steel, we have the luxury of pricing our steel buildings at more competitive rates. You will find that our prices are generally lower than those of traditional construction. That said, the total cost can depend on several factors.
- China’s appetite for steel
- Supply and demand
- Oil and gas prices
- Global production
- Current market conditions
The impact of supply and demand
Similar to other commodities, supply and demand dynamics largely determine the cost of individual metals. China’s growing demand for metals in the past decade has led to a twofold increase in global seaborne iron ore demand, resulting in more volatile price fluctuations. The shift from annual contracts to short-term agreements between steel and mining companies also contributed to this volatility. The economic recovery in Europe and the United States further fueled fluctuations in steel prices too.
Factors that affect the cost of steel buildings
Steel building prices are not set in stone. Many factors can impact your project’s final costs.
The size of your building
Large metal buildings often cost more overall, but their cost of steel per square foot is surprisingly low. Think about it as buying in bulk, as steel building manufacturers often offer lower prices for larger structures. Conversely, smaller buildings may have a higher cost per square foot, but their reduced size can lead to a lower overall price.
Material
Your choice of steel will determine the building’s cost per square foot. Options include:
- Galvanized
- Red Iron
- C-Channel
- Tube Frame
Galvanized steel will be the highest quality, making them popular. They may cost more, but their durability and longevity make them much more cost-effective in the long run. Your building will be more reliable and have better structural integrity, bringing long-term savings.
Your location and climate
Building codes vary from one region to another. At Armstrong Steel, we engineer our prefabricated steel buildings based on your local codes and load-bearing requirements. Depending on your location, you may need more components that add to the total price. This is why we want to know your location when you are looking into a building quote.
Many building codes are based on seismic risk or the risk of an earthquake damaging your property. Southern California has stricter design requirements because it’s prone to earthquakes. Additionally, regional climate can impact our estimate. Buildings in Minnesota and Wisconsin must have high snow loads for safety in the winter. Meanwhile, Florida requires steel structures to withstand high winds and heavy rain as the region is prone to hurricanes.
Level of customization
Customization can significantly impact the pricing of a steel building, as the more specific or complex your design needs, the more the cost will reflect those choices. Customizations such as increasing building dimensions, adding insulation, installing specialized doors or windows, or incorporating aesthetic enhancements like stone façades or unique roof styles can increase both material and labor costs. While basic pre-engineered designs are more cost-effective due to their standardization, custom features tailored to your project add value but also increase overall investment.
However, the flexibility of steel buildings allows you to control these costs by prioritizing which customizations are essential and which can be adjusted based on your budget. In the long run, investing in a customized steel building can save money, as you’re ensuring the structure meets your exact needs without requiring costly modifications later on.
Price your building with Armstrong Steel.
Be sure to work with a reputable fabricator like Armstrong Steel. Our team will work closely with you to provide the best price without compromising aesthetics and functionality. Use our steel building cost estimator or call 1-800-345-4610 for a quote.
Popular Posts
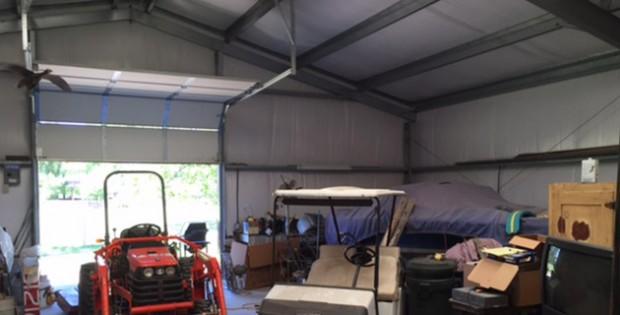
Will Adding a Steel Building Increase My Property Value?
I’ve seen steel buildings increase in popularity every day because builders use these durable, versatile and flexible construction solutions in every application. Not only have homeowners utilized a steel building for residential purposes, but builders have also made additions to their existing property. No doubt that a steel building garage will increase the value of a home, …
Will Adding a Steel Building Increase My Property Value? Read More »
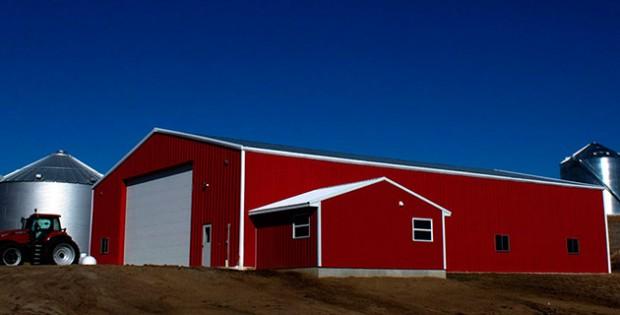
Steel Building Quotes: Get a Grasp on Prices and Estimates
What is the first step of a steel building project, or any construction project for that matter? After you decide to add a new garage, agricultural or commercial building to your property, you’ll most likely start contacting steel building manufacturers for steel building quotes. From there, you can create a timeline for yourself and develop …
Steel Building Quotes: Get a Grasp on Prices and Estimates Read More »
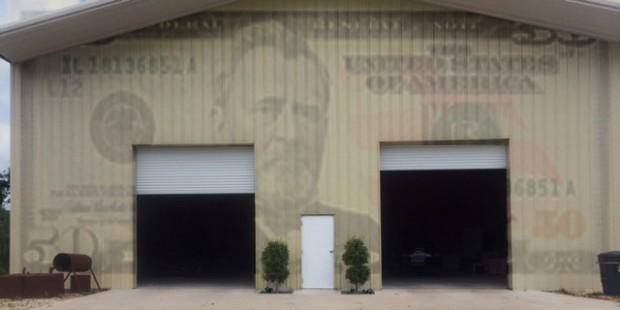
4 Important Factors That Will Impact Your Steel Building Cost
For the past decade, the steel industry has undergone many transformations, and in effect it’s changed the way the construction industry views steel buildings. While the steel itself has been around for hundreds of years, designers and owners of metal buildings are seeing many increased benefits. Because of streamlined processes at manufacturers, energy saving paints …
4 Important Factors That Will Impact Your Steel Building Cost Read More »