Avoid Common Steel Issues When Building Your Warehouse
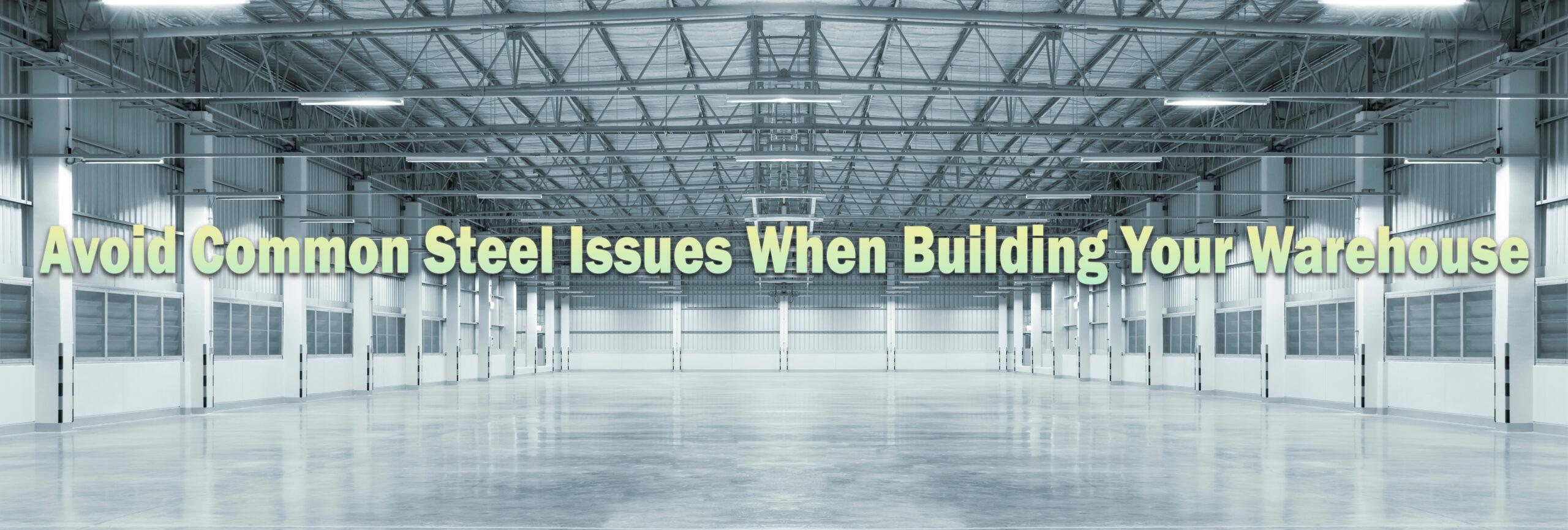
5 Common Steel Warehouse Challenges (And How Armstrong Steel Helps You Avoid Them) Steel buildings are a top pick for warehouses—perfect for storage, manufacturing, or self-storage—because they’re tough, quick to build, and save you money on labor. Picture this: a sturdy structure that goes up fast, ready to hold everything from inventory to heavy machinery. But even with steel’s strengths, things can go wrong if the planning or construction isn’t spot-on. Rust, shaky foundations, or code issues can turn your dream warehouse into a headache.
Luckily, you can dodge these problems by working with a seasoned pre-engineered steel building manufacturer like Armstrong Steel. We’ve been designing warehouses for years, learning the ins and outs of what makes them last, look good, and work well for your business. Some competitors might cut corners or overcomplicate things, but we stick to what’s proven and practical. In this blog, we’ll walk through five common challenges with steel warehouses, explain why they matter, and show how Armstrong Steel tackles them—so you can focus on running your business, not fixing your building.
Challenge #1: Using the Wrong Steel
Steel’s durability is why it’s a warehouse favorite, but not all steel is up to the job. If it’s low-quality or not suited to your area, you could face rust, weather damage, or a structure that can’t hold your load. Imagine a coastal warehouse rusting out in a few years because the steel wasn’t protected right—or a heavy equipment storage buckling under weight it wasn’t built for. Some competitors might offer cheaper steel grades or push fancy coatings you don’t need, leaving you with a building that fails early.
How Armstrong Steel Helps:
We take the guesswork out. Every Armstrong Steel warehouse uses commercial-grade, galvanized steel—the best in the market. The galvanizing adds a zinc layer that fights rust, so it’s ready for tough spots like salty coastal air or industrial zones with chemicals. Our steel’s strength handles anything you store, from light goods to heavy machinery. We don’t make you pick from a confusing list of options; we just use top-tier steel every time. Plus, we engineer each building for your local climate—think humid summers or icy winters—so it’s built to last without extra bells and whistles you won’t use.
Challenge #2: Ignoring Local Building Codes
Building codes keep your warehouse safe and legal, but they’re different everywhere. Skip them, and you’re looking at delays, fines, or even a teardown. A seismic zone might need extra bracing, while a windy area could cap your height. Some competitors might hand you a one-size-fits-all design that doesn’t fit your local rules, leaving you to sort out the mess—or worse, they might not even ask where you’re building until it’s too late.
How Armstrong Steel Helps:
We start with your location. Tell us where your warehouse is going, and we dig into the local codes—seismic zones, wind speeds, snow loads, all of it. Our team engineers your building to meet or beat those standards, no exceptions. For example, if you’re in earthquake country like California, we design for the shakes. In a snowy spot like Minnesota, we account for the weight on the roof. We don’t just slap together a generic plan; we tailor it to your spot, cutting waste and keeping costs in check. You get a warehouse that’s legal, safe, and built right the first time.
Challenge #3: A Weak Foundation
Steel’s strong, but it needs a solid base. A bad foundation can mean sinking, cracking, or long-term damage—especially if your soil’s tricky or you’re storing heavy stuff. Think of a warehouse on sandy ground settling unevenly, or one with forklifts inside cracking a too-thin slab. Some competitors might skimp on foundation planning, assuming any concrete will do, or leave you to figure it out with your contractor, risking mismatches.
How Armstrong Steel Helps:
We don’t build the foundation, but we set it up to succeed. Our engineers design your warehouse with the base in mind, considering your soil—clay, sand, or rock—and what you’ll store inside. We provide detailed drawings and anchor bolt plans so your contractor can pour a foundation that matches perfectly. Need a simple slab for light storage? We’ve got it. Storing heavy machinery? We plan for the extra load. We tie it to local codes, too, so your base isn’t just strong—it’s compliant. You’re ready for a warehouse that stays level and sturdy for years.
Challenge #4: Skipping Ventilation and Insulation
Steel’s energy-efficient, but without good airflow or insulation, you could get stuck with heat buildup or dampness. Too much heat makes workers miserable, and moisture can rust steel or ruin goods. Imagine a warehouse baking in summer with no vents, or wet walls from condensation because airflow was ignored. Some competitors might overlook these details, offering bare-bones designs that save them time but cost you later—or push pricey insulation you don’t really need.
How Armstrong Steel Helps:
We build in the basics to keep your warehouse dry and comfortable. Our designs include ventilation—like ridge vents—to move air and stop moisture from settling in. We figure out what’s right for your building’s size, use, and local weather—no complicated math for you to do. Want extra protection? We make it easy to add simple insulation like fire-rated drywall, which boosts fire resistance and keeps temperatures steady. Our dealers give you a catalog with straightforward options, not a pile of fancy add-ons. Your warehouse stays safe, usable, and hassle-free, whatever the season.
Challenge #5: Installation Mistakes
Even the best warehouse design can falter if it’s a hassle to assemble. Loose bolts, misaligned parts, or sloppy seams might seem minor, but they can lead to leaks, weak spots, or damage down the line—costing you extra time and money to fix. Some competitors might pinch pennies by using flimsy parts or sending vague plans, leaving your contractor frustrated and the job dragging on. That not only bumps up labor costs but can also leave you with a building you can’t fully trust.
How Armstrong Steel Helps:
At Armstrong Steel, we engineer every warehouse with smooth assembly in mind. Our team crafts precise permit drawings—signed and sealed by licensed pros in your state—so your crew has a clear, dependable guide. Every piece arrives pre-cut, numbered, and ready to bolt together with pre-punched holes, all made from commercial-grade steel that’s built to last. We don’t skimp on quality to shave costs; our solid, well-designed components fit perfectly right out of the box.
Our erection guide is like a custom manual for your building—step-by-step and easy to follow. Your beams and columns line up without a hitch because we’ve handled the tough stuff upfront. That means faster setup, lower labor costs, and a warehouse that’s tight and strong from day one. With us, you get a build process that’s straightforward and reliable, no fixes required.
Why Armstrong Steel Makes It Easy
At Armstrong Steel, we don’t just sell you a kit—we deliver a warehouse built for your exact spot and needs. Our commercial-grade, galvanized steel fights rust and stands up to tough conditions. We engineer every building for local codes and seismic zones, plan for a solid foundation, and keep ventilation, insulation, and installation simple and effective. While some might push unnecessary upgrades or skip critical steps, we stick to what works: top-quality steel and smart, practical design. You get a warehouse that’s durable, code-compliant, and ready to work for you—without the stress.
Build your steel warehouse without a hitch
Armstrong Steel will ensure that your steel warehouse project goes smoothly with our careful design process and planning. Whether it has a simple or more elaborate design, our team will work with you and deliver it on time. Call us at 1-800-345-4610 to learn more about our prefab steel buildings, or use the form on this website to price your metal warehouse.
Popular Posts
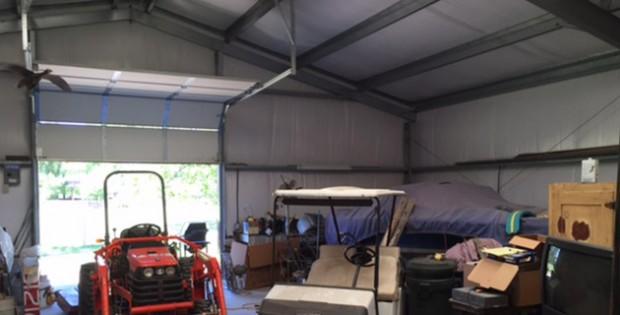
Will Adding a Steel Building Increase My Property Value?
I’ve seen steel buildings increase in popularity every day because builders use these durable, versatile and flexible construction solutions in every application. Not only have homeowners utilized a steel building for residential purposes, but builders have also made additions to their existing property. No doubt that a steel building garage will increase the value of a home,… …
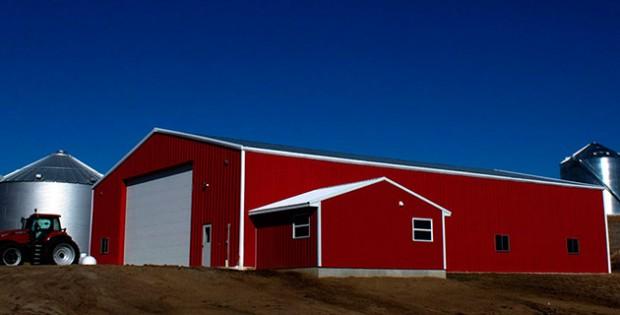
Steel Building Quotes: Get a Grasp on Prices and Estimates
What is the first step of a steel building project, or any construction project for that matter? After you decide to add a new garage, agricultural or commercial building to your property, you’ll most likely start contacting steel building manufacturers for steel building quotes. From there, you can create a timeline for yourself and develop… …
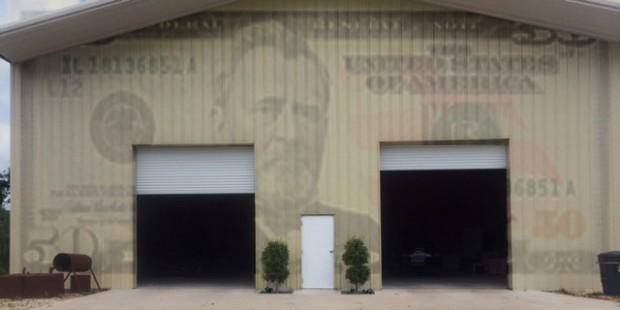
4 Important Factors That Will Impact Your Steel Building Cost
For the past decade, the steel industry has undergone many transformations, and in effect it’s changed the way the construction industry views steel buildings. While the steel itself has been around for hundreds of years, designers and owners of metal buildings are seeing many increased benefits. Because of streamlined processes at manufacturers, energy saving paints… …