Weatherproofing Your Steel Structure: Tips for Extreme Climates
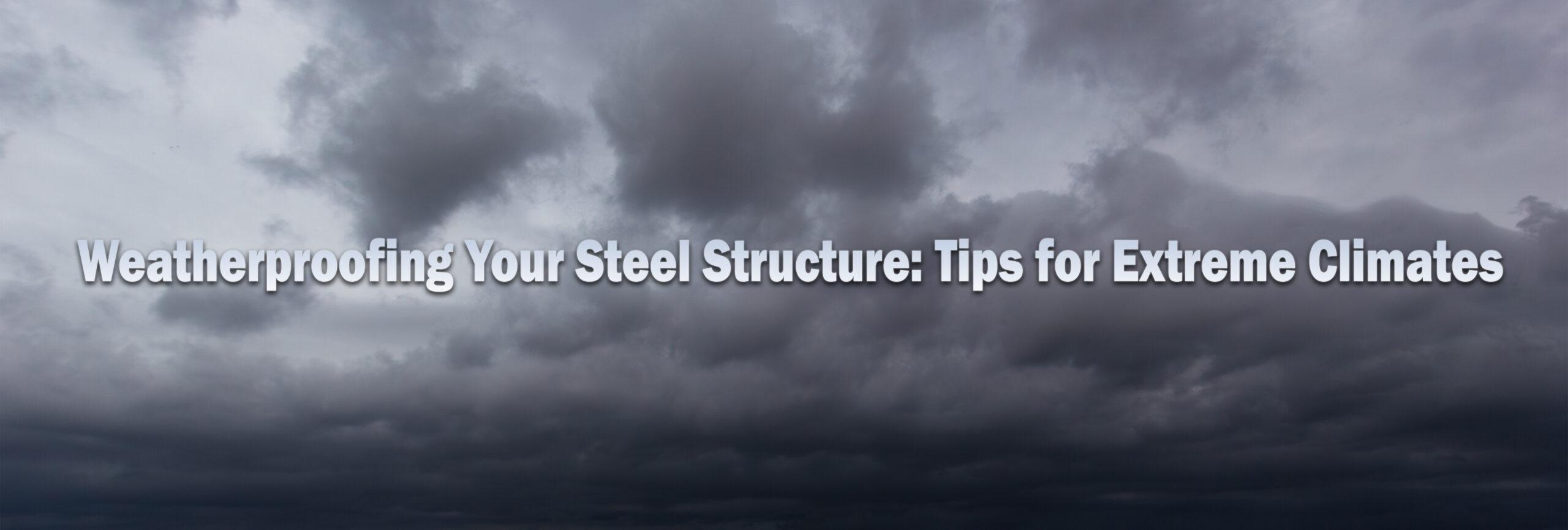
Are you worried about the effects of extreme climate on your building? The best way to ensure a durable and resilient structure is to build with steel. Metal buildings are perfect for extreme environments because they can withstand seismic activity, harsh temperatures, and corrosive agents.
All that said, steel structures still need weatherproofing to prevent damage and maintain integrity. In this blog, we will share tips on how to weatherproof your steel structure to withstand extreme climates. Let’s explore advanced techniques and solutions to build resilient metal buildings that can withstand nature’s most challenging conditions.
Why weatherproof steel structures?
Building with steel brings plenty of benefits, so it’s easy to see why more people are choosing to favor traditional construction. Our prefabricated steel buildings can meet any requirement thanks to their design flexibility. Plus, they’re ready to assemble and erect as soon as they are delivered to your construction site, saving you money and time.
But while steel buildings excel in many areas, extreme climates can make assembly and erection tricky. High temperatures are among their worst enemies. When temperatures rise, metal expands and changes the building’s dimensions. Over time, this can result in structural instability and deformation. In addition, high temperatures can minimize the fire resistance and strength of steel.
Protecting Your Metal Building from Wildfires: Simple Tips
If you’re planning a pre-engineered metal building in a wildfire-prone area, you might wonder how it’ll hold up to heat. At Armstrong Steel, we use commercial-grade steel—the best in the market—so your building starts with top-tier strength. While we focus on delivering a solid structure, there are some easy ways to make it more wildfire-ready. Here’s what you can consider:
- Strong Steel Built In: Our commercial-grade steel is made to handle tough conditions, including the heat of a wildfire. It’s the highest quality we offer, so you’re covered from the start.
- Fire-Rated Drywall: For extra protection, you could add fire-rated drywall inside your building. It’s a simple, affordable way to slow down fire damage and give you more time to deal with a wildfire if it happens.
- Fire Suppression Systems: In a wildfire zone, a basic sprinkler system can make a difference. It sprays water to cool the steel and limit flame spread. We don’t install these, but your building can be set up for a contractor to add one later.
With Armstrong Steel’s commercial-grade quality and a couple of simple upgrades like these, your building can be better prepared for wildfires. Be sure to check local building codes—they might have specific fire-safety rules for your area.
Keeping Your Metal Building Safe from Corrosion: Simple Tips
If your pre-engineered metal building is going into a corrosive area—like near the coast or an industrial site with chemicals—you might be concerned about rust or damage over time. Corrosion can weaken steel if ignored, but at Armstrong Steel, we’ve got you covered with commercial-grade, galvanized steel built to resist it. Here’s how you can keep your building strong in tough conditions:
- Galvanized Steel Built In: Our commercial-grade steel comes with galvanized secondaries—a zinc coating that fights off corrosion right from the start. It’s the highest quality we offer, so your building is ready to handle harsh environments without extra fuss.
- Basic Extra Protection: For added peace of mind in really tough spots, you could add a simple coating like polyurethane paint over the galvanized steel. It’s an easy step to give your building even more defense against things like salt or chemicals.
- Regular Checkups: A quick look at your building every so often can help a lot. Spotting and cleaning off rust or buildup early keeps your steel in great shape and makes it last longer.
With Armstrong Steel’s galvanized, commercial-grade steel and these basic steps, your building is set to stand up to corrosive areas. Check with local pros too—they might have advice tailored to your spot.
Making Your Metal Building Ready for Earthquakes: What to Know
If you’re putting up a pre-engineered metal building in an area with earthquakes, you might wonder how it’ll hold up. Steel is naturally tough—it can bend without breaking, which helps it handle seismic shakes. At Armstrong Steel, we take it further by engineering every building to match your local seismic zones and all the building codes that apply. Here’s how that helps you:
- Designed for Your Area: We don’t just build a standard structure. Our commercial-grade steel buildings are engineered specifically for where you are, factoring in earthquake risks and local rules so your building stays solid when the ground moves.
- Strong and Flexible: Steel’s ability to flex a bit without snapping is a big plus during quakes. We use that strength in every design, making sure your building can take the vibrations and still stand tall.
- Built to Code: Whether it’s seismic forces or other environmental factors, we cover it all. Our team makes sure your building meets or beats the safety standards for your spot, giving you one less thing to worry about.
With Armstrong Steel, you’re getting a building crafted to help handle earthquakes right from the start—no guesswork needed. We use our expertise so you can feel confident in your structure, wherever you’re located.
Extreme weather
Heavy rains, severe storms, extreme heat, and cold—all these can negatively affect your steel structure. High winds can cause torsional forces that may drag and uplift the building. Meanwhile, high humidity and heavy rains cause corrosion. We carefully plan your design while adhering to local building codes and regulations to prevent those problems.
- Increased wind resistance – Adding windshields, cross braces, and horizontal braces can enhance your building’s stability and rigidity against high winds.
- Aerodynamic designs – Enhancing the shape and structure of your metal building can increase its structural load-bearing capacity while minimizing wind resistance.
Material fatigue
Repeated cyclic loading can weaken and eventually cause metal building materials to fail. This phenomenon is known as material fatigue, and it occurs when steel is repeatedly put under stress, even at amounts that don’t seem like they would cause damage on their own. It leads to the formation of small cracks at stress concentration points such as section transitions, bolt holes, and welds.
To mitigate fatigue, steel buildings can be designed with high-strength materials and extended fatigue life considerations. Specialized monitoring systems also allow early detection of minor cracks so that they can be promptly repaired to prevent further damage.
Winterize your steel building
Winterizing metal buildings ensures their resilience in cold weather, whether your area has mild winters or is prone to heavy snowfall and ice. This step starts as soon as we design your structure. Our building consultants will help you choose the right insulation to keep your structure comfortable and protected against extreme cold.
Beyond comfort, winterizing your steel building can also improve energy efficiency and moisture control. Proper insulation and ventilation are crucial for preventing moisture-related problems like mildew, mold, water damage, and rust. These measures also help regulate condensation and humidity throughout the year.
Which insulation is best for your steel structure?
Many types of insulation can help winterize metal buildings. Ultimately, the right choice will depend on your building’s purpose and location. Here are some common materials to insulate your steel structure:
- Rigid boards – Rigid board insulation offers optimum noise dampening and temperature control. It just requires specific construction methods, so talk to us and your metal building contractor for insights.
- Reflective foil – This type of insulation is easy to install and reflects heat away from your building’s exterior to enhance energy efficiency.
- Insulated panels – This solution is made from two metal panels around a foam core layer. Although pricey, it offers unmatched functionality without compromising aesthetic appeal.
- Fiberglass – This insulation is widely used because it’s relatively affordable and easy to install in metal buildings.
More ways to winterize your steel building
While insulation is important for metal buildings, there are other things you can also do to protect your structure’s function and safety all winter.
- Mind the roof – Check your steel structure’s roofing and look for signs of corrosion, holes, missing shingles, and other problems. Inspect the purlins, frames, and joists for wear and tear. Schedule repairs or replacements before winter so your building will be ready when the temperature drops.
- Check the seals – Water can get through the seals along skylights, doors, windows, and other features, so take the time to examine the seals and fix the cracks right away.
- Prevent overgrowth – Check for overgrown bushes and trees that can damage the sides of your building. Keep them trimmed so they won’t scratch the metal panels when high winds blow or during hurricanes.
Designing metal buildings in extreme climates doesn’t have to be challenging. When you have a good understanding of how steel materials behave and your area’s environmental factors, you can navigate the design challenges of metal buildings in extreme climates and implement effective weatherproofing solutions. And don’t worry — you can also count on our building consultants to take the guesswork out of designing your project.
Get in touch with Armstrong Steel
At Armstrong Steel, we want to deliver prefabricated steel buildings that can survive extreme climates. That’s why our team works closely with you to design a resilient, long-lasting structure. We design projects to comply with your local building codes, loads, and environmental factors to ensure their longevity and performance no matter what nature throws at them.
Learn more about weatherproofing steel structures here at Armstrong Steel. You may also call us at 1-800-345-4610 to speak to one of our experts. For a quote, simply click ‘Price My Building’ and share details about your project.
Popular Posts
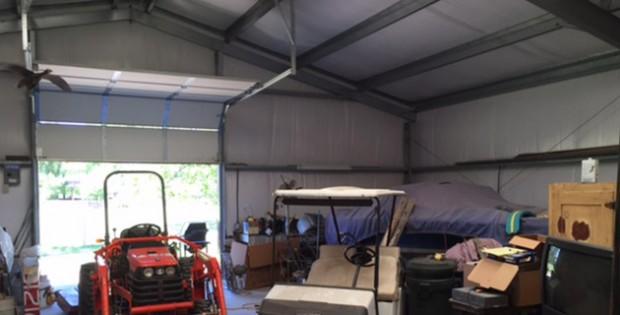
Will Adding a Steel Building Increase My Property Value?
I’ve seen steel buildings increase in popularity every day because builders use these durable, versatile and flexible construction solutions in every application. Not only have homeowners utilized a steel building for residential purposes, but builders have also made additions to their existing property. No doubt that a steel building garage will increase the value of a home,… …
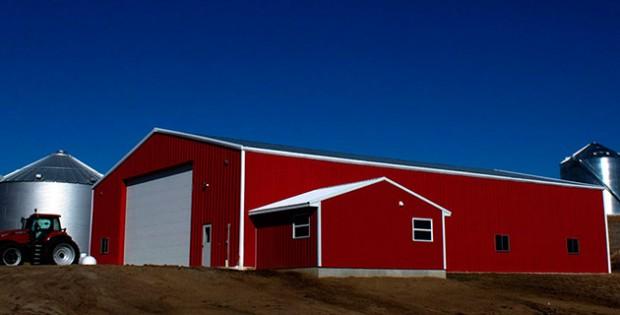
Steel Building Quotes: Get a Grasp on Prices and Estimates
What is the first step of a steel building project, or any construction project for that matter? After you decide to add a new garage, agricultural or commercial building to your property, you’ll most likely start contacting steel building manufacturers for steel building quotes. From there, you can create a timeline for yourself and develop… …
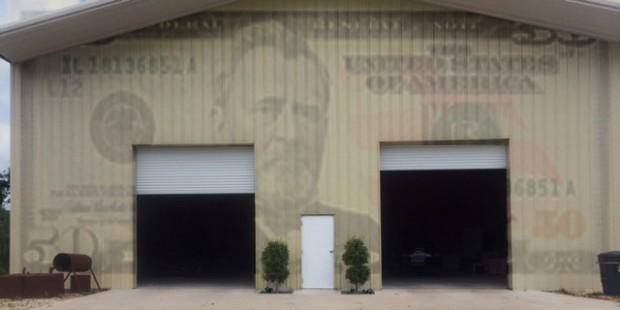
4 Important Factors That Will Impact Your Steel Building Cost
For the past decade, the steel industry has undergone many transformations, and in effect it’s changed the way the construction industry views steel buildings. While the steel itself has been around for hundreds of years, designers and owners of metal buildings are seeing many increased benefits. Because of streamlined processes at manufacturers, energy saving paints… …