Pulling the Curtain Back on Pole Barns
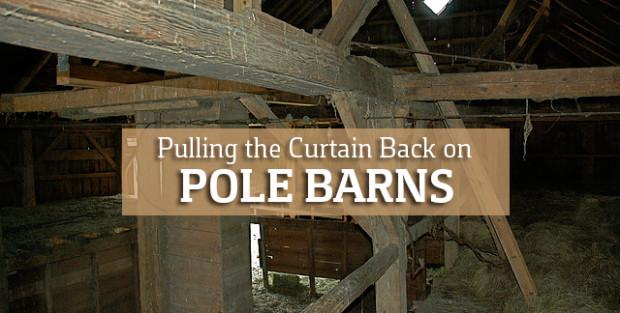
Remember the movie The Wizard of Oz? I think everyone’s seen it so I’m not really spoiling the ending. Near the conclusion of the movie, upon further inspection, we find out that the “great and powerful” Oz is simply man behind the curtain, not a wizard like the characters were led to believe.
Don’t be fooled when it comes to your building project. Pull back your own metaphorical curtain with casual research. In fact, before you start any building project, pole barn, or steel building, examine all the information about every type of construction material and decide which type of building will suit you better.
Longevity
Some pole barns could last for a long time, depending on how well the owner keeps up with them. Wood used in pole barn construction is usually pressure treated, and designed to last for several years. But wood is still susceptible to rot, termites, and insects of all kinds. Pressure treated wood, especially, has the potential to warp or shrink. That leads to screws loosening on purlins and girts (horizontal structural members that support the roof and walls) when the wood bows.
Think about how a pole barn is constructed. Many pole barns don’t require a foundation; the supporting wooden poles are just lowered into the ground. These poles are used as the columns that will eventually support the roof. Depending on the climate and what the wood is exposed to over the building’s lifetime, they might need to be replaced. In addition, pole barns are set directly into the earth. They offer little to no resistance to frost or water heaving. Frost heaving is an upwards swelling of soil during freezing conditions caused by an increasing presence of ice as it grows towards the surface.
Many steel buildings come with a 50-year structural warranty, and don’t require much maintenance or upkeep. Wood, even if pressure treated, will naturally decay because it’s an organic product. Steel will not twist, warp or decay like wood, and will withstand many of the effects of the weather and insects. The parts are engineered to last for decades. Even the paint and wall panels may come with a 40-year warranty and a steel building will retain its “shine” well into the future.
Insurance
A good way to gauge the durability of a building type is as simple as talking to an insurance company. Insurance providers don’t have any preference what type of building you decide to buy; they have no skin in the game. But they will tell you how much it costs to protect your building from a Kansas-sized twister. Insurance companies realize that pole barns have the lowest fire resistance rating and weakest resistance to the elements, so it naturally costs more to insure them. It’s important to insurers that a building is engineered to endure heavy snow and be built to specific seismic and wind loads. Basically, the less likely a building will need structural repair after a storm or weather event, the less it will cost to insure, and the lower insurance rates will be. Steel buildings are designed to survive the harshest weather conditions, and are fabricated specifically for each part of the country. For instance, if you live in Texas, the building you design could look nearly identical to a steel building in Florida, but the difference is the load capacity and the performance of the materials used.
Building Costs
A pole barn might be a cheaper option initially compared to other types of building materials. Like I mentioned before, most pole barns seem cheaper upfront because they require more maintenance and upkeep in the long run. Remember, cheaper isn’t always better. In the construction industry, we say, “you get what you pay for.” Saving money upfront isn’t the best option if you’re only going to spend more money down the road on repairs.
Pole barns are best used when their spans don’t exceed 40 feet. After a design of 40 feet, the cost of the lumber increases exponentially because the structure needs more trusses and cording to stand firm and support the roof of the building. Once your wood building exceeds 40 feet, it will definitely need internal columns for support. In fact, regardless of span, a pole barn will require a truss. That’s more wood for support, which in turn, increases materials and increases cost.
A Steel building can span great distances. This allows you to take full advantage of the interior storage and machinery. When spans surpass 40 feet in steel building design, the costs are much lower compared to pole barns of the same dimensions.
Space
Because of those trusses in the ceiling of a pole barn, the usable amount of space is severely diminished. Plan on storing your farm equipment in your building? What about a tractor-trailer or other storage equipment? While it’s still possible, you’ll have to navigate around interior obstructions, like wood poles.
Instead of poles or truss system, the walls support the roof in a steel building. That’s how a steel building transfers loads to the ground. With clear span framing of a steel building, all the inside space is usable. That presents lots of inventiveness in the design process. Plan on having animals in your building? Design a space for your horses, livestock, and even your trusty dog, Toto. Flying Monkeys? No sweat. You can design the exact type of steel building you want, without planning around your equipment. In a clear span configuration, every foot of the building is at your disposal.
Delivery
One of the last things to consider when choosing a building type is the delivery. Pole barns aren’t difficult to put together, but your “barn” will most likely come to your job site as raw lumber. You can avoid the extra expense of a carpenter to make measurements and shape each piece of timber on site. A steel building will come precut and ready to assemble the moment it’s delivered. You won’t have to make any changes or modifications to the steel components. That’s why it’s called ‘pre-engineered.” All the fabrication work is already done for you. All that’s left is to put the pieces together.
Think with your brain, act with your heart, and have the courage to select the best structure for your property or home. The funny thing about your home is…there’s just no place like it.
Photo courtesy: Putneypics
Popular Posts
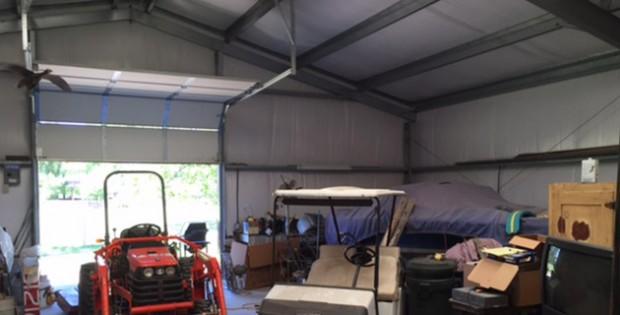
Will Adding a Steel Building Increase My Property Value?
I’ve seen steel buildings increase in popularity every day because builders use these durable, versatile and flexible construction solutions in every application. Not only have homeowners utilized a steel building for residential purposes, but builders have also made additions to their existing property. No doubt that a steel building garage will increase the value of a home,… …
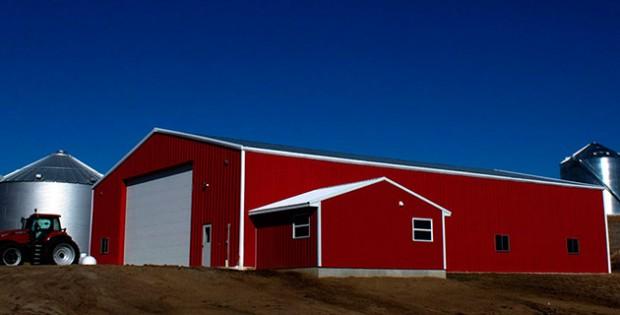
Steel Building Quotes: Get a Grasp on Prices and Estimates
What is the first step of a steel building project, or any construction project for that matter? After you decide to add a new garage, agricultural or commercial building to your property, you’ll most likely start contacting steel building manufacturers for steel building quotes. From there, you can create a timeline for yourself and develop… …
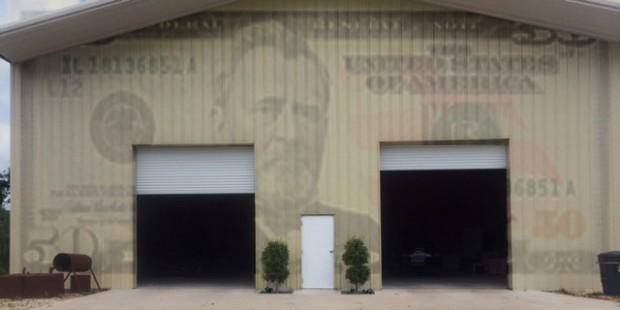
4 Important Factors That Will Impact Your Steel Building Cost
For the past decade, the steel industry has undergone many transformations, and in effect it’s changed the way the construction industry views steel buildings. While the steel itself has been around for hundreds of years, designers and owners of metal buildings are seeing many increased benefits. Because of streamlined processes at manufacturers, energy saving paints… …